自动重订购程序(VM/R2/V2)是如何自动确定安全库存和重订购点的
作者:袁云飞(AlbertYuan)- 微信号yuanalbert
以下内容均为原创,希望对初学者有一些辅助作用,本人主要从事MM/QM/WM的相关工作,不专业处请多多指点,十足干货,码字不易,且行且珍惜,你们的关注就是我努力的动力,转载请引用出处,感激不尽;
When you want a material to be planned by a reorder level procedure you have six standard MRP types available (and you thought it was only four).
Three of these (and you thought it was only two) calculate a reorder level and a safety stock automatically.
The VM simply does so, while the V2 also takes into consideration external requirements - which has no bearing on what we discuss here - and the R2 has an extended lead time because it is only planned according to a set MRP date according to a planning calendar.
All three of these reorder level procedures may have a setting in config which says: “Calculate a reorder point and calculate a safety stock”.
It does so using the forecasting module in the material master. (Note that the forecasting screen has to be maintained for these items).
After you set one of these MRP types and a planned delivery time and a service level in MRP2 you can go to the forecasting screen and execute the forecast calculation.
As a result, the system returns a screen with forecast values (which do not cause MRP relevant requirements), a basic value (the average consumption), an MAD, a reorder point and a safety stock.
If you accept and click to the MRP2 screen you will see that the safety stock value was taken over and in MRP1 you can now see the updated reorder level. How did the system calculate these two values?
First the average consumption of the past periods was determined. This value was multiplied with the replenishment lead time (in external procurement this is purchase order processing time plus planned delivery time plus goods receipt processing time) to set a reorder level which ensures to not run out during the replenishment lead time if we consume exactly the average consumption every day without any variability.
That, of course, never happens and therefore we use a safety stock level by which we lift the reorder point. The safety stock level is now calculated using:
- the mean absolute deviation from the average consumption in the past (MAD; the system created an ex-post forecast and compared the actual consumption figures of the past with the forecast and was able to determine the MAD) - the higher the MAD, the higher the safety stock will be
- the service level from MRP2 - the higher the service level, the higher the safety stock will be
- the lead time - the longer the lead time is, the higher the probability that variability happens and therefore the higher the safety stock
using these parameters, the forecast module is now able to calculate the height of the safety stock and slides it underneath the reorder point in order to raise it.
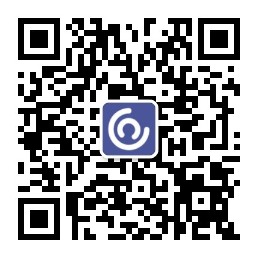
One more thing: if you time-phase your reorder level procedure (R2), the lead time lengthens and therefore the reorder point and safety stock are raised.